Leader, application du variateur de fréquence Harvest dans les moteurs synchrones
2010-1-5 15:56:30
Le variateur de fréquence moyenne tension VFD produit par Leader&Harvest a été mis en service avec succès et mis en pré opération pour conduire le compresseur le 18 avril 2006. Le compresseur CO2 change de couple en fonction de la charge. Il est connu que les moteurs synchrones entraînant un changement de charge sont difficiles à démarrer en douceur et leur vitesse à ajuster. Mais les techniques de production nécessitent un ajustement de la vitesse pour ce genre de charge.
I.Basic data
1. VFD parameters
Model: HARSVERT—S06/130 1250KVA 6kV 50Hz
Production standard:
2. Q/CPBLH003-2004
3. Synchronous motor parameters
Model: TDK1000—48 1000kW/125round/min /116.5A,COSΦ=0.9,ULC=116.5V, ILC=205A
4. Compressor parameters
Model: N—50/200 CO2 compressor
Air discharge: 50m3/min
Shaft power: 880kW
Speed: 125round/min
Absorbing pressure: 1Kg/cm2
Discharge pressure: 201Kg/cm2
Outline dimension: 13145×4646×3750
Cylinder diameter: 920/720/380/210/110(mm)
Net weight: 5000Kg
Piston travel: 800mm
II. Preoperation
According to characters of synchronous motor, we decide to adopt start mode of zero speed variable frequency with exciting current. During starting, exciting current selection is very important.
During operation of piston compressor, its torque pulsation is big and design speed is low. The less speed is, the more pole number of motor is. So electrical angle which is equavalent to space angle of stator and rotor is more. Take an example of motor of 48 pole, a circle of stator and rotor is 24×360=8640º electrical angle. That is, 1 degree of circle is equivalent to 24º electrical angle. Thus, same torque pulsation causes bigger swing of electrical angle, thereby leading to bigger vibration of output current and output power.
In addition, because piston compressor has balance block which assistants to start in direct on line, when balance block drops, compressor is in regenerative state. It is easy to cause VFD DC bus over voltage.
Therefore, variable frequency start is a complicated dynamic course. During starting, selection of each parameter affects whether it can start successfully or not directly.
With excessive excitation current, in the case of idle load light torque, balance block dropping causes rotor field axis ahead of stator field axis. At the moment, synchronous motor is equivalent to synchronous generator. Torque variation of rotor makes synchronous motor equivalent to synchronous generator operation. Because exciting current is big and air gap field is strong, motor will output big power and make VFD trip off due to over voltage fault. We has found the method to solve problem after researching and analyzing.
Secondary, once VFD drives motor to 35Hz upwards, compressor will increase load. At the moment, with stator current rising, rotor exciting current should be big evidently. There is a problem that excessive exciting current causes over voltage, too small exciting current causes synchronous motor out of synchronism, leading to consecutive vibration and trip-off due to over current. After researching and analyzing, we find the answer. We make following process.
1. Operation process of 1# CO2 in fertilizer workshop
1.1 According to idle load test and simulation test with load during 12 th~17 th April, the workshop agreed to make preoperation for #1CO2 VFD with load. Relevant preparedness had taken to ensure it would not occur production accident and equipment accident once fault stand.
1.2 Workshop was ready well. Air fan of VFD room could work. VFD was turned to remote control state.
1.3 During over speed operation, we analyzed technics safety and mechanism intensity of motor and compressor. We confirmed motor and compressor could run stably at 60Hz. According to technics need, speed adjustment range is in 40Hz~60Hz. The frequency can lower to 35Hz when there was need. So output frequency of VFD was set at 35Hz.
1.4 Main process of start/stop (operate as per original process for unmentioned part)
First: add exciting current, start VFD, adjust frequency to 50Hz
Second: increase load gradually, at the same time, raise exciting current gradually (once VFD output current is over 130A, raise 10~20A within limits), till about 100% load. Exciting current is usually controlled at 120A.
Third: adjust speed within limits according to need. Exciting current is following:
Given frequency(Hz) | 60 | 55 | 50 | 45 | 40 | 35 |
Exciting current(A) | 120 | 115 | 110 | 105 | 100 | 95 |
Output current(A) | 105 | 100 | 90 | 80 | 70 | 30 |
Note: output current and exciting current adjustment should be compatible. Above table is reference.
Fourth: close return valve, adjust VFD frequency to meet load variation.
Fifth: once trip-off occurs during operation, operate as per original process.
Sixth: during normal stop, adjust VFD output frequency to 50Hz. Wait load down to 50%, adjust exciting current to appropriate value, stop VFD. Then stop as per original process. Close main switch at last.
1.5 During preoperation, make #2 CO2 drive load to run normally first. #1 CO2 VFD starts and run to 50Hz stably. Then switch load to #1 CO2 compressor slowly. Before this, load of #1 CO2 compressor is false.
1.6 Technics parameters in normal state
Inlet pressure of first section: 4KPa
Outlet pressure of first section: 0.22Mpa
Outlet pressure of two section: 0.84MPa
Outlet pressure of three section: 2.8Mpa
Outlet pressure of four section: 6.6Mpa
Outlet pressure of five section: 20MPa。
2.Electrical circuit
3. Problems and solutions
3.1 During starting, adjust exciting current manually with load increasing. It is easy to cause trip due to over voltage when operation is improper.
3.2 When load is too small, if personnel does not adjust exciting current in time, big swing of output power also leads to trip due to over voltage. Hereto, adopt method of leveling waveform of frequency voltage.
III. Operation record
1. During half year, according to production need, with idea of make high utilization factor of the VFD, total operation time is three months. The longest continuous operation period is 20 days. All records can be get from medium voltage VFD.
2. Data analysis
a. In VFD adjustment mode, there is energy saving effect when frequency is 47Hz downward, and energy saving is in direct rate to frequency lowering.
b. Due to limitation of output capacity of ahead workshop, air supplying of CO2 is more than output air flow of one compressor with full load, and less than that of two compressors. Thus, before reconstruction with VFD, when urea output is big, two compressors usually work. Energy consumption is big. After reconstruction, machine can run to 60Hz, so one motor can meet production need. No need to start another machine. Despite VFD itself has 3% loss, compared with adding a machine, energy saving effect is good. Furthermore, in contrast to adjusting valve opening of two machines, adjusting one motor is more convenient.
c. Adjust load by small potentiometer and do not use valve any more. It is more exact and easier.
IV. Concluding
1. Leader&Harvest VFD drives synchronous motor with variable torque load of CO2 compressor in our plant. It puts into service successfully and runs stably and reliably.
2. In the case of variable technics need, medium voltage variable frequency adjustment for synchronous can save energy. Energy saving effect depends on load. The effect is more evident when load is low. When load is heavy, compared with original mode of two machines work together, energy saving effect is also good.
3. Soft start can avoid big start current impact on power gird. So in the plant which limits start current, motor can start directly without series liquid resistance, avoiding motor not able to start resulted from series liquid resistance.
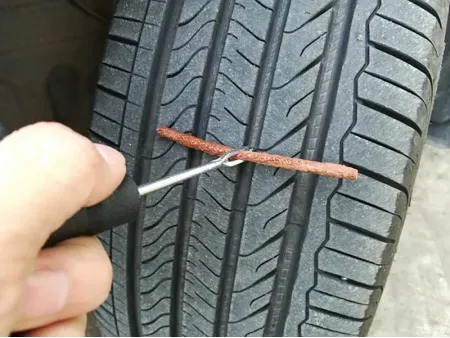