Application du variateur de fréquence moyenne tension dans moteur synchrone
Application du variateur de fréquence moyenne tension dans moteur synchrone
2010-1-5 16:39:15
Résumé : le moteur synchrone moyenne tension est grandement utilisé en raison de ses caractéristiques comme son haut facteur de puissance, sa vitesse stable et son design simple de basse vitesse. Mais un parcours physique compliqué et une contrôlabilité difficiles ont restreins les applications du variateur de fréquence VFD avec le moteur synchrone. Leader&Harvest a résolu les problèmes principaux via de nombreuses analyses théoriques, tests et simulations. Leader&Harvest a appliqué avec succès un variateur de fréquence moyenne tension VFD sur un moteur synchrone de 1000kW/6kV dans la centrale à ammoniac de Jvhua Company en avril. Cet article vous expose l’application.
1.Preface
Medium voltage synchronous motor is widely used as its characters of high power factor, stable speed and low speed simple design, such as fan, water pump, oil pump and so on. For big power low speed load, such as mill and compressor, using synchronous motor not only heightens power factor, but also leaves out variable-speed gear. It lowers system fault rate and simples maintenance.
Because of complicated physical course and difficult controllability of synchronous motor, original speed adjustment system used to install speed/position sensor, which increases fault rate and lowers system reliability.
Cell-cascaded multi-level VFD has been applied widely on medium voltage asynchronous motor as its predominances of low price, high power factor, small harmonic, no distortion of output voltage and high rebiability. Adopting VFD on synchronous motor will enhance system reliability effectively. It can reduce cost of synchronous motor reconstruction and heighten energy saving. In the mean time, it develops a new wide market for VFD. Leader&Harvest has applied medium voltage VFD on 1000kW/6kV synchronous motor in Ammonia Plant of Jvhua Company successfully in April. This article will state the application case.
2. Excitation input during starting in direct on line
When power voltage drives synchronous motor to run in direct on line directly, excitation input is a complicated course. When armature winding medium voltage switch is on, auxiliary contact of medium voltage breaker informs excitation device to prepare excitation input. At the moment, excitation device insert a deexcitation resistor on excitation winding automatically to avoid medium voltage inducted, meanwhile, supplys some start torque during starting. After armature winding power on, under joint function of start winding and excitation winding which connects to deexcitation resistor, motor starts to accelerate. When speed reaches to 95% of synchronous speed, excitation device chooses appropriate timing of excitation input according to induction voltage of excitation winding. Motor is switched to synchronous speed operation. If salient effect of synchronous motor is strong, start load is low, motor has been in synchronous speed operation before excitation device in search of appropriate timing of excitation input. In this case, excitation device will make excitation input as per regulation of delay-excitation input, that is, force excitation input after15s of medium voltage switch power on.
3. Synchronizing process when VFD drives synchronous motor to start
When VFD drives synchronous motor to run, start mode is different from above mode. It is : start up with excitation.
Before VFD outputs voltage to synchronous motor stator, namely before starting, excitation device outputs some current to excitation winding of synchronous motor first, then VFD outputs appropriate voltage to armature winding of synchronous motor to start motor.
Main difference of synchronous motor differing from asynchronous motor is that during operation of synchronous motor, included angle of armature voltage vector and rotor pole position must be in some range, otherwise system loses synchronizing. At early of motor start, the included angle is optional and it must be controlled in some range by appropriate synchronizing. Then motor enters in synchronous operation state. Therefore, synchronizing is key problem.
Following processes are synchronizing course during starting.
First, excitation device outputs some exciting current to excitation winding of synchronous motor, builds a magnetic field on synchronous motor rotor.
Second, VFD forces DC voltage on armature winding of motor, creating some stator current. at the moment, some stator current creats on synchronous motor and builds strong magnetic field on stator. Rotor begins to rotate by rotor stator electromagnetic force. Rotor pole moves close to different terminals of stator pole gradually. At the moment, rotating direction of rotor may be same as direction of motor normal operation, may be opposite.
Third, VFD rotates voltage vector which forces on armature winding slowly as per rotating direction of motor normal operation. With rotating of motor rotor and stator magnetic field, rotor pole will sweep different poles of stator in certain moment, or, rotor pole catches up with rotating stator pole. At the moment, rotor pole is absorbed reliably by stator pole. After vibration with a little damping , angle between the two is near to small constant gradually. By now, motor enters synchronous speed operation state. Synchronizing finishes.
Fourth: VFD adjusts output voltage as per pre-set acceleration and V/F curve, and accelerates to given frequency gradually. At the moment, rotor angle of motor enlarges to certain constant gradually. Then under absorbing of stator magnetic field, rotor pole accelerates to expected speed gradually. Start-up finishes.
During synchronizing course, selection of stator rotor magnetic potential and switch of each process are key. If choose stator magnetic field which is too low, stator pole can not be absorbed reliably when it passes different poles of rotor at first time. After that, with reverse accelerating action of same pole repulsion, the two will have more relative speed when rotor passes different poles of stator next time. Stator magnetic field can not drive rotor pole further, which leads to synchronizing fault eventually. Choosing stator magnetic field which is too big may lead to stator iron core saturation, and lead to over current of VFD.
Typical start process of synchronous motor is following:
4. Stable operation and excitation adjustment
VFD drives synchronous motor without speed/position sensor. Output waveform of VFD is multi-level PWM waveform mostly, same as waveform when it drives asynchronous motor, so VFD is equivalent to a sine voltage power source with high reliability, no torque pulsation.
Reactive current of synchronous motor flows just between VFD and motor, without admitting to enter power grid, so no need to control exciting current exactly. Generally, adjust exciting current manually in typical working condition. Make output current of VFD minimum, output power factor near to 1, then keep this current unchanged during adjusting. For working condition which needs to adjust exciting current instantly during operation, VFD can measure reactive power which outputs from VFD to motor, send excitation signal to excitation device, adjust exciting current.
5. Fault deexcitation of synchronous motor
During normal stop, VFD drives motor to decelerate to stop speed, then stop supplying voltage to armature winding of motor. At the speed, inducted voltage of biggest exciting current at stator side is less than withstand voltage of transformer output side. So during free sliding afterwards, keeping exciting current would not damage equipment, no need for deexcitation immediately.
In the case of fault, just stop to supply voltage to armature winding but keep exciting current, rotating motor will output three phase AC voltage to its stator consecutively, damaging equipment safety. Therefore, when there is serious fault and needs stop, VFD has to inform excitation device to make deexcitation.
Physical course of deexcitation is following:
At early of deexcitation, exciting current lowers quickly by excitation device action. But main magnetic flux of motor can not change suddenly, big current is inducted on damping winding. At the moment, rotating motor outputs medium voltage to stator (VFD output side). Then current of damping winding decelerates to zero gradually, stator voltage also decelerates gradually. The attenuation usually needs several seconds. So output of VFD must be with ability of standing short time over voltage in stop state.
6. Application introduction of ammonia plant
Ammonia Plant of Jvhua Company was established in 1959. It is important fertilizer manufacturer. The reconstruction is for 1# CO2 piston compressor in urea workshop. Some parameters in following:
Model | N-50/200 |
Rated shaft power | 880 kW |
Rated speed | 125 r/min |
Cylinder level | 5 level |
Discharge flow | 50 m3 / min |
Outlet pressure | 201 kg / cm2 |
Motor of compressor is 1000kW/6kV synchronous motor
Rated voltage | 6000 V |
Rated current | 116.5 A |
Rated power | 1000 kW |
Rated power factor | 0.9 |
Rated frequency | 50 Hz |
Connecting | Y |
Rated exciting current | 205 A |
Rated speed | 125 r/min |
Pole number | 48 |
The plant selects HASVERT-S06/130 VFD. Scheme is “one drive one” manual bypass circuit.
During operation in direct on line, QS1 and QS2 are open, QS3 is closed. Implement start, operation and stop as per original logic.
During variable frequency operation, QS3 is open, QS1 and QS2 are closed. When VFD is power on, breaker QF is closed. After 15s, excitation device inputs exciting current to motor, then sends command of “start” to VFD. VFD outputs voltage as per preset logic. Motor starts.
During stop, site sends command of “stop” to VFD. VFD drives motor to decelerate to stop frequency, then stops supplying voltage. Break QF at last. Auxiliary contact informs excitation device to make deexcitation. After finishing deexcitation, turn off power source of excitation device.
When there is fault, VFD stops voltage output, meanwhile, break QF immediately. Auxiliary contact informs deexcitation instantly.
7. Concluding
Successful application of VFD on synchronous motor extends application field of medium voltage VFD, and also extends way of energy saving, provides more technology guarantees for building a economized society.
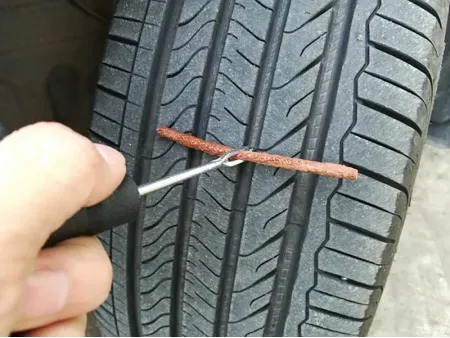